Classification of alloy steel
According to alloy element content
Low alloy steel (total alloy element is less than 5%), medium alloy steel (total alloy element is 5%-10%), high alloy steel (total alloy element is higher than 10%).
According to alloy element composition
Chromium steel (Cr-Fe-C), chromium-nickel steel (Cr-Ni-Fe-C), manganese steel (Mn-Fe-C), silicon-manganese steel (Si-Mn-Fe-C).
According to small sample normalizing or cast structure
Pearlite steel, martensitic steel, ferrite steel, austenite steel, ledeburite steel.
According to use
Alloy structural steel, alloy tool steel, special performance steel.
Alloy structural steel
The steel used to manufacture important engineering structures and machine parts is called alloy structural steel. There are mainly low alloy structural steel, alloy carburizing steel, alloy quenched and tempered steel, alloy spring steel, and ball bearing steel.
Low alloy structural steel
1. Uses: Mainly used in the manufacture of bridges, ships, vehicles, boilers, high-pressure vessels, oil and gas pipelines, large steel structures, etc.
2. Performance requirements
(1) High strength: Generally, its yield strength is above 300MPa.
(2) High toughness: The elongation is required to be 15% to 20%, and the room temperature impact toughness is greater than 600kJ/m to 800kJ/m. For large welded components, higher fracture toughness is also required.
(3) Good welding performance and cold forming performance.
(4) Low cold brittle transition temperature.
(5) Good corrosion resistance.
3. Composition characteristics
(1) Low carbon: Due to the high requirements for toughness, weldability and cold forming performance, its carbon content does not exceed 0.20%.
(2) Add alloy elements mainly composed of manganese.
(3) Adding auxiliary elements such as niobium, titanium or vanadium: A small amount of niobium, titanium or vanadium forms fine carbides or carbonitrides in steel, which is conducive to obtaining fine ferrite grains and improving the strength and toughness of steel.
In addition, adding a small amount of copper (≤0.4%) and phosphorus (about 0.1%) can improve corrosion resistance. Adding a small amount of rare earth elements can desulfurize and degas, purify the steel, and improve toughness and process performance.
4. Commonly used low-alloy structural steels
16Mn is the most used and produced steel in my country's low-alloy high-strength steel. The structure in use is fine-grained ferrite-pearlite, and the strength is about 20% to 30% higher than that of ordinary carbon structural steel Q235, and the atmospheric corrosion resistance is 20% to 38% higher.
15MnVN is the most used steel in medium-grade strength steel. It has high strength, and good toughness, weldability and low-temperature toughness. It is widely used in the manufacture of large structures such as bridges, boilers, and ships.
When the strength level exceeds 500MPa, ferrite and pearlite structures are difficult to meet the requirements, so low-carbon bainite steel was developed. Adding elements such as Cr, Mo, Mn, and B is conducive to obtaining bainite structure under air cooling conditions, making the strength higher, and the plasticity and welding properties are also better. It is mostly used in high-pressure boilers, high-pressure containers, etc.
5. Heat treatment characteristics
This type of steel is generally used in the hot-rolled air-cooled state and does not require special heat treatment. The microstructure in the use state is generally ferrite + troostite.
Alloy carburizing steel
1. Uses It is mainly used to manufacture machine parts such as transmission gears in automobiles and tractors, camshafts, piston pins on internal combustion engines, etc. These parts are subjected to strong friction and wear during work, and at the same time bear large alternating loads, especially impact loads.
2. Performance requirements
(1) The surface carburized layer has high hardness to ensure excellent wear resistance and contact fatigue resistance, and has appropriate plasticity and toughness.
(2) The core has high toughness and sufficiently high strength. When the toughness of the core is insufficient, it is easy to break under impact load or overload; when the strength is insufficient, the brittle carburized layer is easy to break and peel off.
(3) Good heat treatment process performance At high carburizing temperature (900℃~950℃), austenite grains are not easy to grow and have good hardenability.
3. Composition characteristics
(1) Low carbon: The carbon content is generally 0.10%~0.25%, so that the core of the part has sufficient plasticity and toughness.
(2) Add alloy elements to improve hardenability: Cr, Ni, Mn, B, etc. are often added.
(3) Add elements that hinder the growth of austenite grains: mainly add a small amount of strong carbide forming elements Ti, V, W, Mo, etc. to form stable alloy carbides.
4. Steel types and grades
20Cr low hardenability alloy carburizing steel. This type of steel has low hardenability and low core strength.
20CrMnTi medium hardenability alloy carburizing steel. This type of steel has high hardenability, low overheat sensitivity, and a relatively uniform carburized transition layer, with good mechanical properties and process performance.
18Cr2Ni4WA and 20Cr2Ni4A high hardenability alloy carburizing steel. This type of steel contains more elements such as Cr and Ni, has high hardenability, and has good toughness and low-temperature impact toughness.
5. Heat treatment and structural properties
The heat treatment process of alloy carburizing steel is generally direct quenching after carburizing, and then low-temperature tempering. After heat treatment, the structure of the surface carburized layer is alloy cementite + tempered martensite + a small amount of residual austenite structure, with a hardness of 60HRC~62HRC. The core structure is related to the hardenability of the steel and the cross-sectional size of the part. When fully hardened, it is low-carbon tempered martensite with a hardness of 40HRC~48HRC; in most cases, it is troostite, tempered martensite and a small amount of ferrite, with a hardness of 25HRC~40HRC. The toughness of the core is generally higher than 700KJ/m2.
Alloy quenched and tempered steel
1. Application Alloy quenched and tempered steel is widely used in the manufacture of various important parts in automobiles, tractors, machine tools and other machines, such as gears, shafts, connecting rods, bolts, etc.
2. Performance requirements Most quenched and tempered parts are subjected to a variety of working loads, and the stress conditions are relatively complex, requiring high comprehensive mechanical properties, that is, high strength and good plasticity and toughness. Alloy quenched and tempered steel is also required to have good hardenability. However, the stress conditions of different parts are different, and the requirements for hardenability are different.
3. Composition characteristics:
(1) Medium carbon: The carbon content is generally between 0.25% and 0.50%, with 0.4% being the most common;
(2) Adding elements such as Cr, Mn, Ni, Si, etc. to improve hardenability: In addition to improving hardenability, these alloying elements can also form alloy ferrite and improve the strength of steel. For example, the performance of 40Cr steel after quenching and tempering is much higher than that of 45 steel;
(3) Adding elements to prevent the second type of temper brittleness: Alloy quenched and tempered steel containing Ni, Cr, and Mn is prone to second type of temper brittleness when tempered at high temperature and slowly cooled. Adding Mo and W to steel can prevent the second type of temper brittleness. The appropriate content is about 0.15% to 0.30% Mo or 0.8% to 1.2% W.
4. Steel types and grades
(1) 40Cr low hardenability quenched and tempered steel: The critical diameter of oil quenching of this type of steel is 30mm to 40mm, and it is used to manufacture important parts of general size.
(2) 35CrMo medium hardenability alloy quenched and tempered steel: The critical diameter of oil quenching of this type of steel is 40mm to 60mm. Adding molybdenum can not only improve the hardenability, but also prevent the second type of temper brittleness.
(3) 40CrNiMo high hardenability alloy quenched and tempered steel: The oil quenching critical diameter of this type of steel is 60mm-100mm, and most of them are chromium-nickel steel. Adding appropriate molybdenum to chromium-nickel steel not only has good hardenability, but also can eliminate the second type of temper brittleness.
5. Heat treatment and microstructure performance The final heat treatment of alloy quenched and tempered steel is quenching plus high temperature tempering (quenching and tempering treatment). Alloy quenched and tempered steel has high hardenability and is generally oil-cooled. When the hardenability is particularly high, it can even be air-cooled, which can reduce heat treatment defects.
The final performance of alloy quenched and tempered steel is determined by the tempering temperature. Generally, 500℃-650℃ tempering is used. By selecting the tempering temperature, the required performance can be obtained. In order to prevent the second type of temper brittleness, rapid cooling (water cooling or oil cooling) after tempering is conducive to improving toughness.
The microstructure of alloy quenched and tempered steel after conventional heat treatment is tempered troostite. For parts that require wear resistance on the surface (such as gears and spindles), induction heating surface quenching and low-temperature tempering are performed, and the surface structure is tempered martensite. The surface hardness can reach 55HRC~58HRC.
The yield strength of alloy quenched and tempered steel after quenching and tempering is about 800MPa, and the impact toughness is 800kJ/m2. The core hardness can reach 22HRC~25HRC. If the cross-section size is large and not quenched, the performance will be significantly reduced.
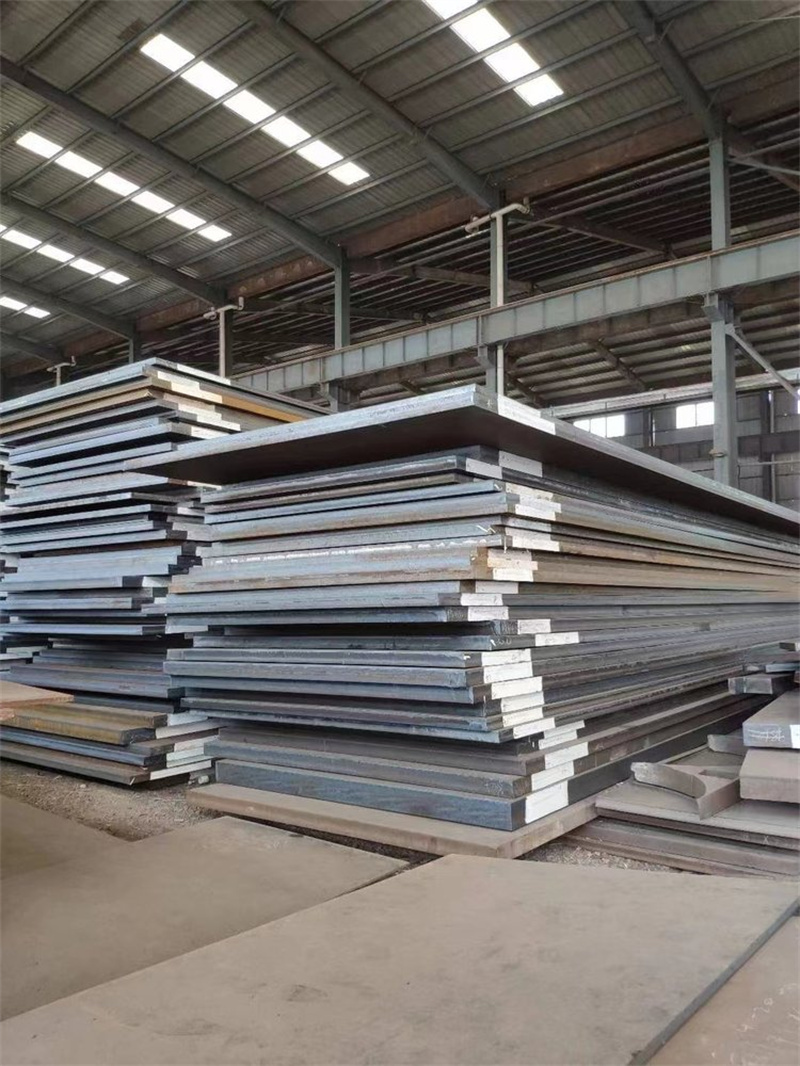
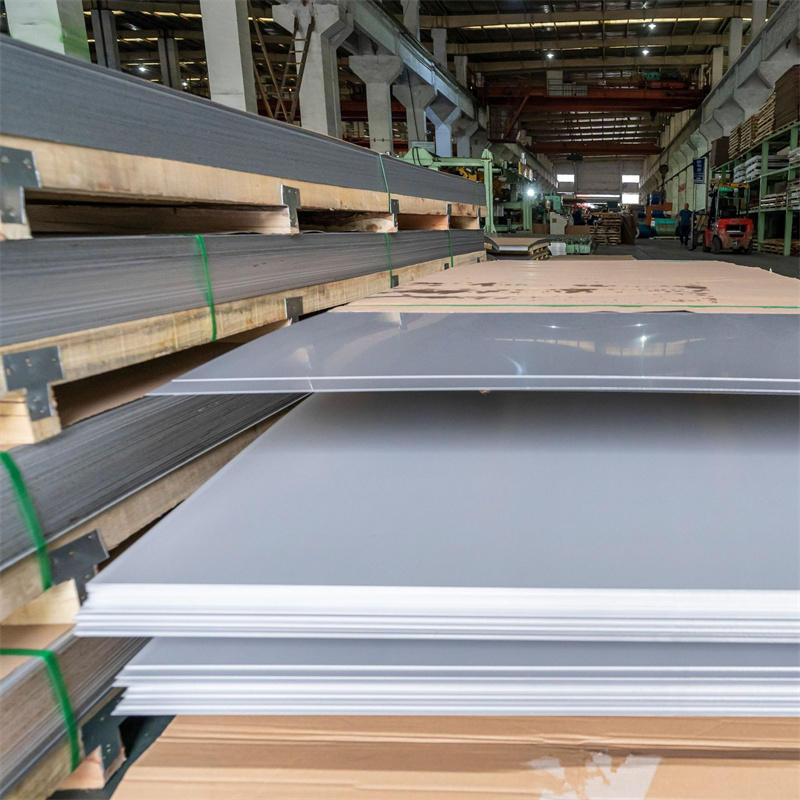
Post time: Mar-01-2025